Wing Technology
The Worlds Most Advanced Sponson and Inflatable Boat Construction
All Wing sponsons and boats are essentially hand built one at a time in our Northern California Factory. Armed with the most advanced materials on the planet and our custom built, proprietary software, your Wing design, engineering, and production team has been setting new standards in fit, performance, and durability for the past three decades.
Our Computer Aided Design or CAD program is the only one of it's kind in the world; custom-built for Wing. This software streamlines the process of tube design taking into account unique polyurethane stretch along the horizontal, vertical and diagonal axis for a tighter fit, higher performance and better looks. With this software Wing pioneered the higher performing and lighter weight 'tapered tube' over 20 years ago at a time when other manufacturers where still using software more commonly used to design home ducting systems.
Our heat welded seams offer a virtually indestructible bond, fusing the polyurethane material in a 1.5" seam that is far stronger than the original fabric. Our Competitors glued seams have a shelf life that over time can become brittle and fail to adhere.
The Wing Inflatables Path to Success:
The process from raw materials to finished product
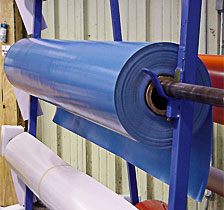
Materials
We start by inspecting every lot of polyurethane material to make sure that it meets our specifications. Samples from every lot are weld-tested to make sure the coating and the base fabric are properly bonded to each other. Every roll is measured for the appropriate thickness with a micrometer and various lots are accurately weighed. A square yard of 40 oz. fabric should weigh 40 ounces. As fabric is rolled out on the cutting table it is inspected for any cosmetic blemish and if found, rejected. All other hardware is visually inspected and sampled for appropriate attributes.
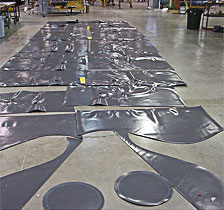
Cutting
Once the design specs are determined on our end, and confirmed and approved by the customer, they are entered into our design software. Information is sent to the plotter-cutter wand cuts out the polyurethane patterns. We cut only one layer of fabric at a time so every piece is visible for inspection as it is being cut. Upon completion of the cutting, handles, d-rings, line loops, etc. are then chemically fused with a bonding technique after the pattern pieces are welded together. The pores of the polyurethane need to be opened up and softened by applications of heat and solvents so as to create a chemical bond with the adhesive. Adhesive is applied on both surfaces to be bonded and allowed to set.
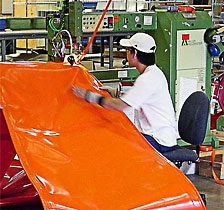
Seam Welding
Rotary welders are used to put pattern pieces together that make up the air-holding tube or foam sheath. Using hot air, with a 1.5" overlap, pushing material forward similar to sewing, a bubble or bead of molten polyurethane is formed between the two layers of material just before they are rolled through compression wheels and fused together.
A thermo-welded seam, as opposed to a glued seam, results in far tougher, longer-lasting tubes. Thermo-welding fuses the over-lapped layers into one solid piece creating a seam that will not fail over time as a glued seam will.
Once the tube has been closed and sealed it goes through rigorous US Coast Guard certified, air holding tests to determine air-loss rates and validate the integrity of the tube.
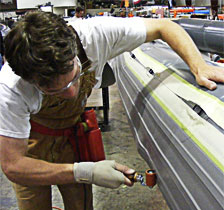
Finishing
Once a sponson has been approved for air-holding, it moves to the finishing department. It is in finishing that the high-density, low-migration PVC rub strake or rub rail is installed. The critical placement of the attachments that marry the tube to the hull are precisely located and bonded in place. Top and bottom chafe are installed and any other accessories such as texture, handles, life-lines, color patterns and custom logos are added.
Upon approval from Final QA the tubes are ready for packaging and shipping from our plant in Northern California.
Why Polyurethane?
Polyurethane is the strongest air-holding material available. The fabric consists of two layers of thermoplastic extruded film that is chemically bonded to a specified woven base fabric, creating a tough, durable, puncture-resistant fabric.
Polyurethane offers superior:
- Abrasion Resistance
- UV Resistance
- Tear and Puncture Resistance
- Highly Inert, Resting Chemical Damage
- Compatible with Both Heat and RF Welding
read more:
Polyurethane vs. Hypalon